THE PROJECT
The salinometer probe has been completely redesigned based on the dimensional standards of a sample probe supplied by the customer. The aim of the project was to raise the quality of the product by increasing the operational life cycle, the accuracy in reading information and the versatility of use. Consistent with our team working method, Ergo Design took care of every engineering phase, while ItalMeccatronica dealt with prototyping, mass production and testing of finished products through quality tests.
THE PRODUCT
The probe consists of a main body from which two electrodes come out. When the probe is in operation, the electrodes come into contact with water and allow the measurement of electrical conductivity. The inside of the probe body houses a electronic board that allows the data detected by the probe to be stored and interfaced with the display that is part of the equipment. The electronic circuit, completely redesigned by us, includes a thermal compensation system that allows to always have an exact reading of the conductivity value even in different temperature conditions. Above the probe body is screwed the cap equipped with a watertight cable gland so that water and humidity cannot enter the product.
The salinometer probe has been completely redesigned based on the dimensional standards of a sample probe supplied by the customer. The aim of the project was to raise the quality of the product by increasing the operational life cycle, the accuracy in reading information and the versatility of use. Consistent with our team working method, Ergo Design took care of every engineering phase, while ItalMeccatronica dealt with prototyping, mass production and testing of finished products through quality tests.
THE PRODUCT
The probe consists of a main body from which two electrodes come out. When the probe is in operation, the electrodes come into contact with water and allow the measurement of electrical conductivity. The inside of the probe body houses a electronic board that allows the data detected by the probe to be stored and interfaced with the display that is part of the equipment. The electronic circuit, completely redesigned by us, includes a thermal compensation system that allows to always have an exact reading of the conductivity value even in different temperature conditions. Above the probe body is screwed the cap equipped with a watertight cable gland so that water and humidity cannot enter the product.

MATERIALS
The salinometer probe is a precision instrument capable of working under continuous use conditions, with high performance rates and very precise tolerances, and it‘s a full part of a product category in which we have been working for years: design for work. Given the reliability and precision required by the equipment used, we have maintained a high quality product standard.
The electrodes are CNC machined and galvanically treated, nickel-plated and gold-plated. Gold is used because it’s stable, doesn’t corrode and guarantees an always optimal conductivity reading. The cap and the probe body are CNC machined and the material used is Nylon charged with fibreglass, because it’s more robust and less subject to dimensional variations than simple Nylon. Finally, the gaskets are made of Viton, a material that resists better at high and low temperatures compared to the nitrile rubber commonly used in gaskets.
ASSEMBLY
Thanks to the design architecture used, the assembly process is quick and easy. The probes are placed in heated racks, kept at a temperature of about 40°C by a self-regulating system. In the racks the probes dry and reach the temperature to be able to pour the epoxy resin that seals the electronic board and connections inside the object. In this way humidity and water cannot compromise the functioning of the product. Once the resin is dry, the assembly is completed by positioning the gasket, the brass washer that protects the probe from the stresses on the assembly seat and finally the cap.
The salinometer probe is a precision instrument capable of working under continuous use conditions, with high performance rates and very precise tolerances, and it‘s a full part of a product category in which we have been working for years: design for work. Given the reliability and precision required by the equipment used, we have maintained a high quality product standard.
The electrodes are CNC machined and galvanically treated, nickel-plated and gold-plated. Gold is used because it’s stable, doesn’t corrode and guarantees an always optimal conductivity reading. The cap and the probe body are CNC machined and the material used is Nylon charged with fibreglass, because it’s more robust and less subject to dimensional variations than simple Nylon. Finally, the gaskets are made of Viton, a material that resists better at high and low temperatures compared to the nitrile rubber commonly used in gaskets.
ASSEMBLY
Thanks to the design architecture used, the assembly process is quick and easy. The probes are placed in heated racks, kept at a temperature of about 40°C by a self-regulating system. In the racks the probes dry and reach the temperature to be able to pour the epoxy resin that seals the electronic board and connections inside the object. In this way humidity and water cannot compromise the functioning of the product. Once the resin is dry, the assembly is completed by positioning the gasket, the brass washer that protects the probe from the stresses on the assembly seat and finally the cap.
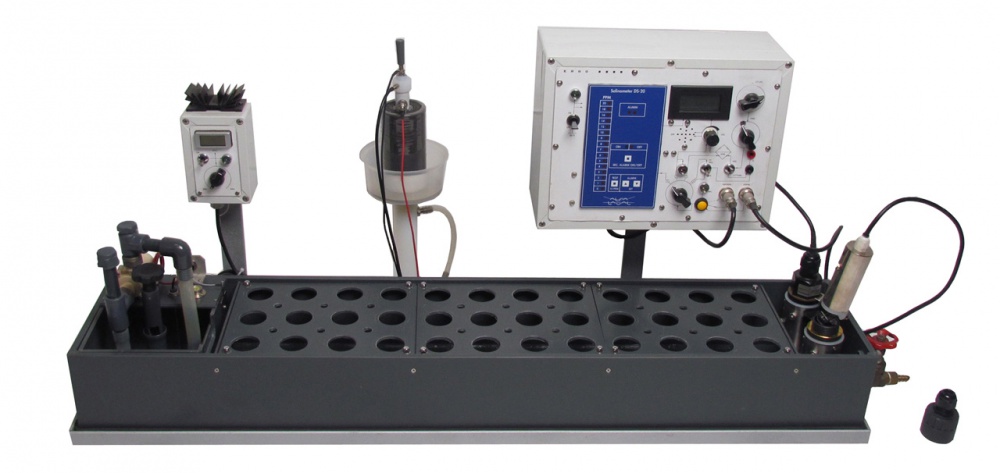
COLLAUDE
After assembling the electrodes and electronic cards, the probes are placed on a tank containing continuously flowing demineralised water. Every single probe is checked and tested in order to deliver perfectly working parts to the customer. In order to test the final products we have designed and manufactured a special salinometer that conducts quality tests on the probes, guaranteeing safe and constant operating precision. To keep the salt content in the tank constant, we have designed and manufactured an electrolytic dialyzer, which stabilizes the salt concentration in the water at a value of about 10 ppm.
At one end of the tank we have created a reading station where it’s verified that the probes have no defects and function correctly. The values read by each probe are compared with those detected by the sample probe. If the values read by the probe are anomalous, the control panel of the quality control system allows to carry out a series of checks and discover any defects.
IMPROVEMENTS
Compared to the sample probe supplied by the customer, we have made the following improvements:
Durability: the conscious choice of stronger materials has improved the robustness;
Ergonomics: the shape of the cap ensures a safer and easier grip;
Reliability: the intervention on materials and electronics has increased the accuracy;
Versatility: electronics of the probe allows further functions to be implemented in future;
Cost: the simplicity of production and assembly has enabled cost containment.
After assembling the electrodes and electronic cards, the probes are placed on a tank containing continuously flowing demineralised water. Every single probe is checked and tested in order to deliver perfectly working parts to the customer. In order to test the final products we have designed and manufactured a special salinometer that conducts quality tests on the probes, guaranteeing safe and constant operating precision. To keep the salt content in the tank constant, we have designed and manufactured an electrolytic dialyzer, which stabilizes the salt concentration in the water at a value of about 10 ppm.
At one end of the tank we have created a reading station where it’s verified that the probes have no defects and function correctly. The values read by each probe are compared with those detected by the sample probe. If the values read by the probe are anomalous, the control panel of the quality control system allows to carry out a series of checks and discover any defects.
IMPROVEMENTS
Compared to the sample probe supplied by the customer, we have made the following improvements:
Durability: the conscious choice of stronger materials has improved the robustness;
Ergonomics: the shape of the cap ensures a safer and easier grip;
Reliability: the intervention on materials and electronics has increased the accuracy;
Versatility: electronics of the probe allows further functions to be implemented in future;
Cost: the simplicity of production and assembly has enabled cost containment.